Sealcoating is a very cost-effective way to protect your asphalt. It also prolongs the life of your pavement and improves its appearance. It is important to understand the different types of sealcoats before making a decision.
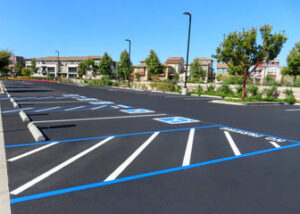
The surface must be completely dry for the application of a seal coat. You should not apply it if rain is forecast within 24 hours of the application. Visit https://www.rochesternysealcoating.com/ to learn more.
When it comes to Sealcoating, there are several different methods that can be used. One of the most common is coal tar emulsion, which can be used on asphalt and concrete surfaces. However, this type of Sealcoat isn’t ideal for commercial properties, due to its toxicity and environmental risks. The other option is petroleum-based, which is a much safer alternative to coal tar. However, it’s also not as effective and can leave the surface looking dull and worn down.
Coal tar is a byproduct of the coking, liquefaction, or gasification of coal. It is also known as coal-tar pitch, tar black, or bitumen. It can be used for various purposes, including making electrical insulation and electrodes for aluminum and steel arc furnaces. It is also used in manufacturing chemical products, such as pesticides and rubber tires. Coal tar is toxic and carcinogenic. It also has a very unpleasant odor. It is a dark liquid that looks similar to asphalt and has a sticky consistency. It is sometimes mixed with clay to make it less viscous.
It was once a major source of income in Scandinavia, especially in Finland, where it was primarily produced from pine. It is still used in some traditional Finnish medicines for its microbicidal properties, and as a flavoring for candy and alcohol. It was also used to preserve wooden ships against rot.
The most serious problem with coal-tar-based sealcoat is that it releases PAHs (polycyclic aromatic hydrocarbons). These are harmful to humans and cause cancer, lung problems, and other health issues. Studies have shown that coal-tar-based sealcoat can be the source of up to 80 percent of the PAHs in urban stream and lake sediments. Coal tar-based sealcoats are also linked to increased levels of PAHs in house dust, which is a significant route for exposure in young children.
Asphalt emulsion
Asphalt emulsion is an environmentally friendly and cost-effective alternative to hot-mix asphalt. It can be used in various applications, including paving and road repair. It can also be applied to driveways and parking lots. It is available in a variety of formulations, and it can be mixed with other materials to create custom asphalt products. The proper application of asphalt emulsion is crucial for long-term pavement performance and durability.
The main component of asphalt emulsion is water. The emulsifying agent stabilizes the asphalt particles and keeps them from coalescing into a continuous asphalt mass. The type of emulsifying agent affects the rheological properties of the resulting emulsion, as well as its compatibility with aggregates.
In addition to the emulsifying agents, asphalt emulsions may contain additives for specific purposes. For example, some additives improve the resistance of asphalt emulsion to weathering. Others slow down the degradation of asphalt emulsion by UV radiation. In some cases, these additives can even repair existing damage to asphalt surfaces.
When selecting an emulsion, consider its charge designation, which begins with “C” for cationic or “A” for anionic. The next number indicates how fast the emulsion sets, or coalesces into a continuous asphalt mass. The standardized designations are RS (Rapid Set), MS (medium set), SS (slow set), and QS (quick set).
Some newer asphalt emulsions are designed with nano-materials that improve their mechanical properties, such as tensile strength and resistance to deformation. These new chemistries can also enable asphalt emulsions to self-heal and repair minor cracks and imperfections autonomously. Precise temperature control during the blending process is vital for preventing premature breaking of the emulsion. Vacuum emulsification, a growing technology in the industry, allows asphalt emulsion to be blended at reduced atmospheric pressure, which reduces air bubbles and volatiles that can degrade the resulting material.
Coal tar emulsion
Coal tar emulsion is the traditional asphalt sealcoating material. It has been around for decades and offers a high level of pavement protection. However, it is now being phased out due to its environmental and health-related risks. While it still provides an effective means of extending the life of your asphalt, other types of sealcoating are more sustainable and safer for the environment.
The main ingredient in coal tar is refined coal tar, which is a thick black liquid that has long been used in the sealcoating industry. It has been the go-to product for many years because it is a durable and cost-effective solution to protect asphalt from weathering and typical deterioration.
However, recent concerns about the harmful effects of coal tar have prompted some municipalities to ban its use. Coal tar is known to contain large amounts of polycyclic aromatic hydrocarbons, or PAHs. These are known to cause cancer and have been found to be toxic to wildlife, including fish and birds. It is also caustic and can cause skin burns if it comes into contact with your skin.
As a result of these concerns, there is a growing movement to switch to an alternative to coal tar sealcoat. Fortunately, there are several options available for contractors who want to make the switch. One option is asphalt emulsion, which is made from recycled oil products. It can be mixed with coal tar to produce a darker sealer. The advantage of asphalt emulsion is that it is safe for the environment, has low PAH levels, and does not emit fumes or odors. In addition, it dries quickly and provides an attractive flat black finish that looks brand-new.
Fast-dry
Sealcoating involves applying a new layer of asphalt material to the surface of the pavement. It can be used to repair cracks and voids in the surface, and it also helps to protect the pavement from weather damage. In addition, it can enhance the appearance of the road or parking lot. However, it is important to remember that the new coating needs to be properly cured before being subjected to vehicle traffic. This can take up to three days and is influenced by ambient conditions. Ideally, the best time to seal is in spring and summer when the humidity levels are lower. This allows the air to evaporate more easily, making the process faster.
In addition, workers need to be adequately protected while working with sealcoating materials. These chemicals are carcinogenic and can be harmful if they come into contact with the skin or lungs. They should wear long-sleeved shirts, pants, impervious boots and gloves and safety goggles. They should also read the material safety data sheet provided by the manufacturer before using the product.
Adding additives to a sealcoating mixture can help to improve its performance and durability. These can include fillers, rubberizers, and other compounds. They can improve the viscosity and elasticity of the asphalt paving material, and they can be useful for prolonging the life of the sealcoat. However, these products cannot replace the use of the right mix design for the project and the application of the material in accordance with its specifications.
Choosing the correct type of sand is also crucial. The sand must be of the proper grade to produce the desired traction and texture. It should also be free of dust and small pebbles.
Acrylic
Acrylic sealcoats provide excellent protection for concrete surfaces. They block harmful UV rays and resist fading, which means they’ll last longer than other types of seal coats. This type of sealcoat is also more flexible than others, which can help it withstand temperature changes.
Before applying acrylic sealcoat, it’s important to read the manufacturer’s instructions for proper application. Using the wrong tools or methods can damage the surface, and can also lead to problems like clouding, peeling, bubbling, and blistering. In addition, you should only apply the sealcoat during dry weather. This is to avoid wasting materials and to allow the sealcoat to dry properly.
While coal tar and asphalt emulsions are the most popular options for seal coating, there are also other choices. These include polyurethanes, which are similar to acrylic but have a different resin. The main advantage of polyurethanes is that they’re more durable and chemical-resistant than acrylic sealcoats. However, they’re more expensive and require a higher level of skill to apply.
Acrylic sealcoats are a good choice for smaller parking lots and sports courts, because they offer high-quality protection without the environmental dangers of coal tar. They can also be applied in a variety of colors, which can help identify specific areas or add a sheen to the concrete surface. This makes them a great option for commercial property owners, as they can protect their parking lot from chemicals and debris. However, these coatings tend to have a shorter lifespan than coal tar and asphalt emulsions. This may mean that you’ll need to reapply them more frequently than other types of sealcoats. The most common signs that it’s time to reapply a sealcoat are pitting and degradation of the substrate or surface. If you notice these signs, it’s best to contact a professional for advice and services.